Losing Margin on an Integrated Manufacturing Process
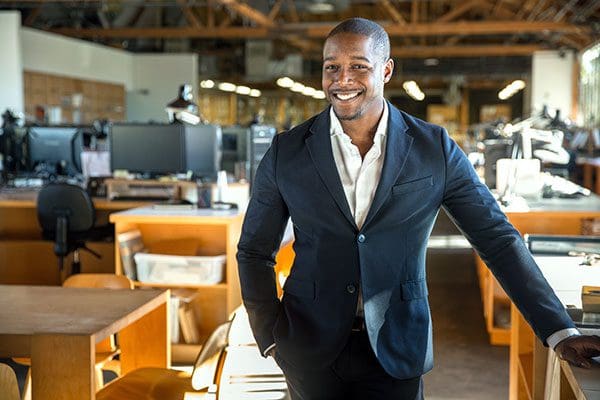
Often, companies that sell fully integrated products (manufacturing/assembly, warehousing, and shipping) under-report their total cost of sales. This can lead to incorrectly pricing the product and wasting important operating profits.
In the gross margin, inventory cost is commonly referred to as product cost. However, what may not be very well known is the importance of including all manufacturing and assembly costs. The following costs are related to this process:
Expected Costs:
- Labor
- Materials
- Overhead
Costs or situations that can be overlooked:
- Labor availability – a small pool of workers means higher costs and turnover
- Building costs such as rent, utilities, maintenance, and insurance
- Property and real estate taxes – Inventory levels and location lead to higher taxes
- Equipment rental, repairs, parts, and supplies
- Depreciation on manufacturing and assembly assets
- Labor turnover – staff in training means longer processing times and higher scrap rates
- Separate labor expense to identify Regular time, Overtime and Labor Earned to best evaluate absorption rates
- Consumable costs that are not used as raw materials like glue, water, grease, etc.
To ensure the right information is included in the product cost, process reviews should be conducted regularly.
Review on a regular basis – changes to:
Raw Materials / Components – Landed Cost (Cost + freight & duty/fees), Units of Measure
Changing purchase prices of components due to things like MOQs (minimum order quantities) or lead times can make freight more expensive. To make sure the inventory costs are properly valued; a company should review the landed cost frequently. In order to achieve this, it is advisable to use standard costing in order to let the noise slip through the cost of inventory and to achieve a more balanced approach to inventory costs.
BoM (Bill of Materials) Set Up – Substitutions or Components
Substitutions may be agreed upon in product design and marketing, but not passed along to the BoM builders, which often affects the financials either in scrap costs or in advertising costs to remarket the product.
Assembly Builds – Time studies for the build tasks. Updated labor costs. Build scrap and consumables.
Assembly builds labor costs can vary greatly, so it is important to monitor them closely. Regular time studies should be conducted to determine the correct absorption rate. Turnover on the floor is an important factor when comparing the time it takes, and the number of mistakes (scrap) for a skilled worker and a trainee. Consumables and scrap can vary if they are purchased from different sources, so update the standard cost if a permanent change occurs or set a standard that is averaging the costs.
PPV and Labor Earned accounts – Actual purchase and labor cost versus the standards
Depending on the product manufactured, the number of PPV accounts to be examined monthly or at the very least quarterly will vary. Expenses for freight in, duty, consumables, and standardized packaging may be included in these accounts. Labor Earned should be evaluated on a monthly basis to see how efficiently the manufacturing floor is being used and whether standard labor rates need to be raised due to wage increases.
In conclusion, cutting costs will raise your margin, but understanding the whole product cost, which allows a company to appropriately price a product for consumer sale, will also increase the margin.